
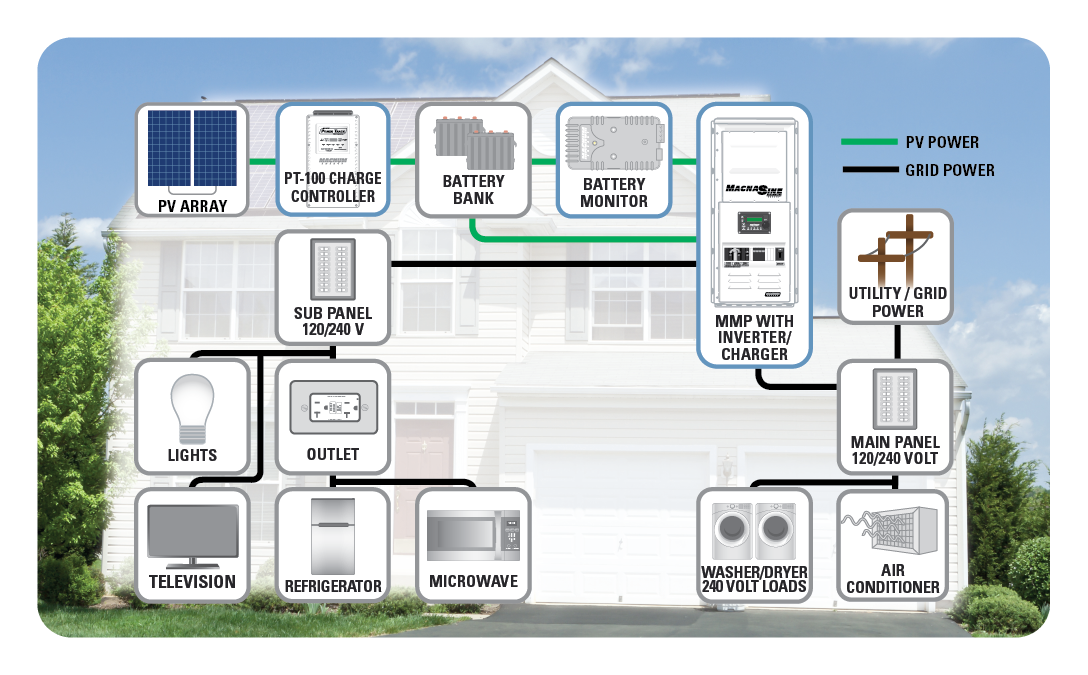
- #Connecting to renogy inverter to converter software#
- #Connecting to renogy inverter to converter code#
The next diagram (Figure 2) depicts the components and connections to power an AC load. Otherwise, for our controllers that don’t have this terminal lug, you can connect an equipment ground directly to the controller enclosure. If you need an equipment ground for any metal parts on a controller enclosure, some of our controllers include an equipment ground terminal lug.
#Connecting to renogy inverter to converter code#
This meets NEC code requirements for grounding. Therefore, it is possible to establish a common negative ground for the entire system: the solar array, controller, battery and the load. This is because all our PWM and MPPT controllers have a common negative ground. You’ll notice that the battery is grounded at the negative battery terminal.

During the evening when there is no sunlight, battery power is used to run the load.
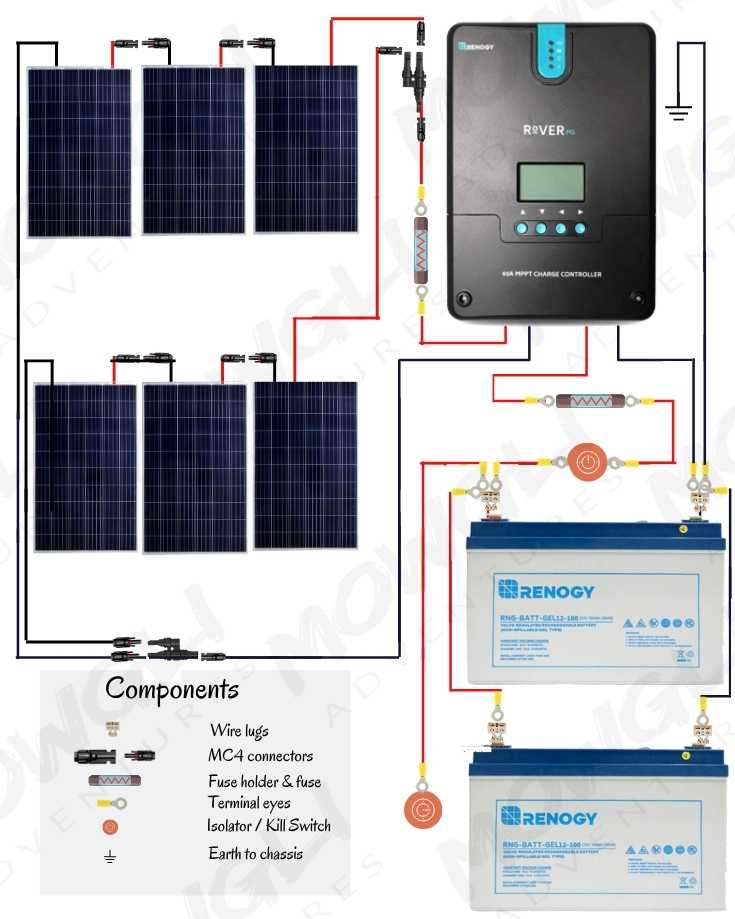
The charge controller regulates the amperage and voltage that is delivered to the loads and any excess power is delivered to the battery system so the batteries maintain their state of charge without getting overcharged. In the wire diagram schematic above with DC load, sunlight contacts the solar modules, which convert solar into DC electrical power that it delivers to a charge controller. Connections between battery, load, PV array, and the controller should have disconnect switches to enhance safety and facilitate ease of installation and breakdown. The battery provides power to the controller so always make sure that solar and loads are disconnected before connecting or disconnecting the battery from the controller. When disconnecting, you reverse that order. When installing a solar charge controller, it is recommended that you connect and disconnect in the following order: You can use the best PV modules, batteries, wiring, and loads, but their capabilities will be restricted by the quality of the charge controller. So, the small amount of money you might save deploying a cheaper charge controller will pale in comparison to the money and time wasted on battery replacement. The charge controller generally represents about 10% of your total off-grid power system costs, whereas batteries can be about 40% of your first-time cost and 80% of your lifetime costs. The best solar charge controllers extend battery life for many years beyond their normal life expectancy, whereas inferior controllers cause premature battery failure and can render your PV system inoperable. A poor controller can cause battery failure, and complete failure with your entire solar system. You can have the best batteries and best modules in the world, but they’re only as reliable as your controller. Most people don’t see or recognize these dramatic voltage and current changes going on within their controllers, but if they did have the scopes and sophisticated monitors that could show what is actually happening, they could tell which controllers are going to have the best effect on battery life. Battery and PV voltage and current can change in split seconds and the power electronics in the controller must be able to respond fast enough to accommodate these changes.
#Connecting to renogy inverter to converter software#
Reliable charging to maintain battery health and extend battery life is affected by how well, and how fast, the controller’s software controls the electronic component hardware.
